From a story by Mitchell Keller on the Construction Briefing websitewww.constructionbriefing.com : – The most used manmade substance on the planet has evolved over millenniums, but the next decade of… Read More
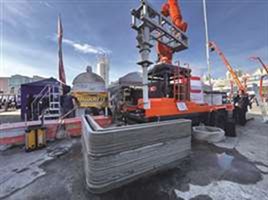
From a story by Mitchell Keller on the Construction Briefing websitewww.constructionbriefing.com : – The most used manmade substance on the planet has evolved over millenniums, but the next decade of… Read More
WHEN COVID-19 disruptions caused inflation to shoot up, so did the cost of building new homes. So, as inflation returns to normal, why are construction costs accelerating again? It’s a… Read More
Concrete dominates the urban construction environment and has significant impact inrural area as well. Understanding the types and characteristics of concrete and bestusage is essential for industry planners and enterprises…. Read More
In a presentation to a World of Concrete event in the USA recently, Michelle Wilson, senior director of concrete outreach and support at the Portland Cement Association looks at the… Read More
While concrete has always been a primary material on job sites, its popularity poses a problem for those advocates seeking greener construction methods and building products to reduce the impact… Read More
Cesco is proud to introduce to the Agi market Cesco Australia Ltd is thrilled to announce the release of our latest organic concrete remover innovation – COR Super Gel. After… Read More
– an evidence based analysis of demand against the market’s capacity to deliver our country’s public infrastructure pipelines – from Infrastructure Australia. Overall, public infrastructure demand has flattened compared to… Read More
Engineers Just Made Concrete 30% Stronger. The Secret Ingredient? Coffee. Spent coffee grounds (SCG) are the most wasteful byproduct of the entire coffee industry. By one estimate, 60 million pounds… Read More
Cesco is proud to announce the release of COR daily wash – Cesco Organic concrete remover Revolutionizing Concrete Cleaning Cesco Australia Ltd is thrilled to announce the release of our… Read More
Hallam Blast & Spray Booth open for Business 🎉 Exciting news – featuring our brand new, purpose-built, industrial-sized spray booth at Cesco Australia’s Hallam Blast and Spray Facility! 🎉 We’re… Read More